Wind Tower
Wind towers are essential structures in renewable energy production, specifically for wind power. These towers harness kinetic energy from air flow, using it to rotate turbine blades and drive a generator that produces electricity.
1. Wind Tower Overview
Wind towers are essential structures in renewable energy production, specifically for wind power. These towers harness kinetic energy from air flow, using it to rotate turbine blades and drive a generator that produces electricity. A wind tower is a critical support structure that not only stabilizes the turbine but also absorbs vibrations, ensuring efficient energy transfer and prolonging the turbine's lifespan. Given its role, the wind tower must meet strict manufacturing standards to ensure structural integrity and operational safety.
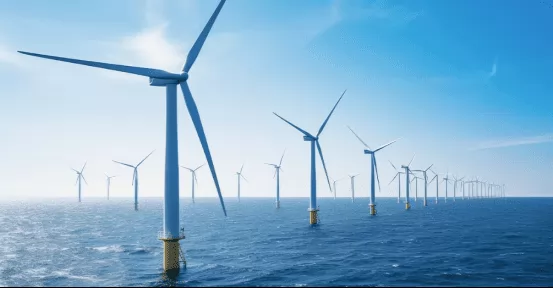
Wind Tower Specifications and Technical Standards
-
Dimensions and Materials: Wind towers are generally manufactured in sections ranging from 50 to 120 meters in height. The steel used is typically high-strength, corrosion-resistant carbon or alloy steel, which meets international standards like ASTM A572 and EN 10025 for mechanical properties and durability.
-
Design Standards and Load-Bearing Requirements: Wind tower design must adhere to international standards such as IEC 61400 (wind turbine safety) and DNV GL-ST-0126, ensuring resilience under extreme wind loads, fatigue stress, and environmental conditions. Towers are designed to withstand seismic activities and to bear significant axial and lateral loads without compromising structural integrity.
-
Aerodynamic Efficiency: The aerodynamic properties of wind turbine blades are optimized for maximum energy conversion. Blades are crafted with a specific airfoil profile to increase lift and reduce drag, enabling more efficient kinetic energy transfer from wind to rotational energy. Blade material often includes reinforced composites for durability and minimal weight.
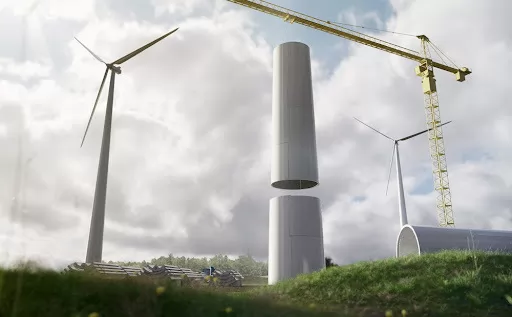
2. Detailed Wind Tower Production Process
-
Cutting and Grooving: The manufacturing process begins with cutting steel plates using CNC cutting equipment. For plates thicker than 16mm, grooving is applied, enhancing weld penetration and fit precision. Consistency at this stage is vital to ensure seamless alignment during the welding process.
-
Precision Rolling and Forming: Rolled steel plates are subjected to various forming stages to achieve the desired roundness and diameter. To ensure dimensional accuracy, any detected deviations are corrected through secondary shaping, followed by rigorous roundness and diameter inspections.
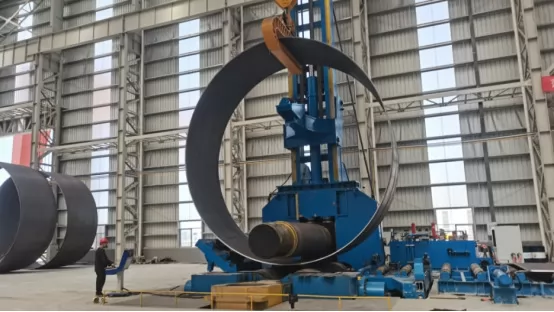
-
Longitudinal and Circumferential Welding: Welding rotators and fitup growing lines assist in securing cylindrical sections for both longitudinal and circumferential welds. These equipment systems ensure proper alignment and stable rotation, resulting in highquality welds for the structural integrity of the tower.
-
Quality Control Measures: Besides straightness and flatness checks, nondestructive testing (NDT) methods like ultrasonic testing (UT) and radiographic testing (RT) are conducted. These tests detect potential internal defects, ensuring that all welded joints meet safety standards.
-
Final Steps: After welding, additional quality checks such as flange welding, sandblasting, and painting are performed. Nondestructive inspection validates welds, while sandblasting ensures the surface is ready for a protective coating. The final step involves assembling internal components and preparing the tower for transport to the installation site.
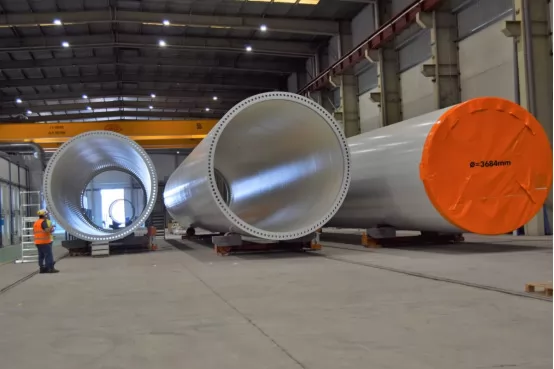
3. Automation Equipment for Welding and Positioning
-
Welding Manipulators: Welding manipulators provide a stable and adjustable platform for automated welding tools, supporting inner and outer seam welding with precision. With multiaxis rotation and adjustable arms, they enable precise welding on both curved and flat surfaces.
-
FitUp Growing Line Systems: Fitup systems hold and adjust the cylinder sections, allowing for seamless alignment and height, distance, and angle adjustments. The system’s synchronized rotation and alignment make it ideal for handling large components, such as those used in wind towers.
-
SelfAligning Welding Rotators: Selfaligning rotators are designed to automatically adjust based on the pipe or cylinder size. With polyurethane or steel wheels, these rotators secure the cylinder, preventing slippage during welding and supporting various wall thicknesses.
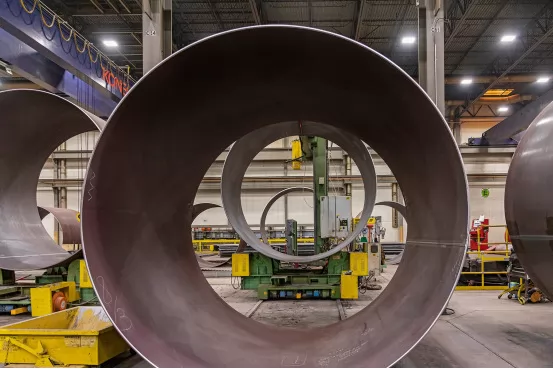
-
Hydraulic FitUp Rigs: Hydraulic fitup systems enable multidimensional adjustments of cylinder sections, streamlining assembly for large towers. Equipped with remote control capabilities, they allow precise positioning without manual intervention.
-
Advanced Welding Techniques: Techniques like laser welding and submerged arc welding (SAW) are commonly used in tower manufacturing for their highspeed, precision, and deep penetration qualities. Laser welding minimizes heat distortion, making it ideal for materials that require minimal postprocessing.

4. Advanced Welding Techniques in Wind Tower Production
-
Submerged Arc Welding (SAW): SAW is widely used for welding large steel structures, offering deep weld penetration and smooth finish with minimal spatter. Its high deposition rate is advantageous for thickwalled sections, making it ideal for the heavy steel components in wind towers.

-
Gas Metal Arc Welding (GMAW): Also known as MIG welding, GMAW provides control over heat input and arc stability, essential for precise welds in thinner sections or components requiring tight tolerance.
-
Laser Welding: Laser welding is valued for its high precision and minimal heat distortion. In wind tower production, it is often used for sections where precision is paramount, and it minimizes postprocessing by reducing warping. Laser welding also enables joining of dissimilar metals, which can be beneficial in multimaterial structures.
-
Safety Standards and Regulatory Compliance: Welders and automation equipment comply with ISO 3834, which sets quality requirements for welding. Additionally, occupational health and safety guidelines (OSHA 1910 for the U.S., EN ISO 15085 in Europe) ensure that automated welding processes reduce operator exposure to hazards.
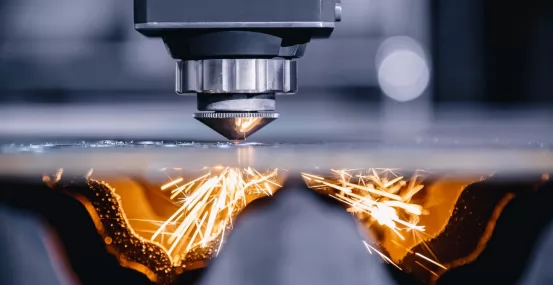
5. Automation in Quality Control for Wind Towers
-
Automated NonDestructive Testing (NDT): Advanced automated NDT systems include ultrasonic testing robots that inspect welds for internal flaws. Vision systems and laser scanning technologies are also used to assess surface quality, ensuring weld integrity and adherence to dimensional tolerances.
-
Automated Inspection and Data Collection: Integration between welding and inspection robots allows realtime data monitoring, where each weld is digitally recorded and evaluated for quality. This automated feedback loop enables immediate adjustments, minimizing defects and rework.
-
Dimensional Inspection and Roundness Control: Laser measuring systems assess tower section roundness and straightness throughout production. These measurements ensure structural stability and proper alignment during assembly, facilitating seamless onsite installation.
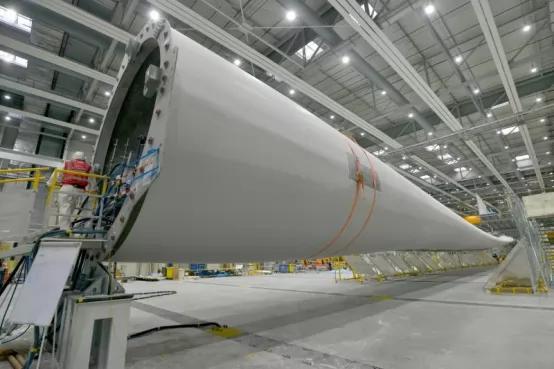
6. Expanded Use Cases and Specifications for Foundation Pipes
-
HighPressure and Offshore Pipeline Specifications: For extreme conditions, foundation pipes must meet standards like API 5L for highpressure applications. Offshore foundation pipes require additional coating treatments for corrosion resistance, such as fusionbonded epoxy (FBE) or threelayer polyethylene (3LPE) coatings.
-
CorrosionResistant Coatings and Treatments: Coatings play a critical role in pipeline longevity, especially in harsh environments. Techniques like cathodic protection and internal linings prevent corrosion, with protective layers designed to endure UV exposure, saltwater, and chemical abrasion.
-
Industry Standards and Testing Requirements: Foundation pipes comply with standards such as ASTM A106 for seamless carbon steel pipes, essential for hightemperature applications. Hydrostatic testing, radiographic inspection, and dye penetrant testing are some of the rigorous quality assessments performed.
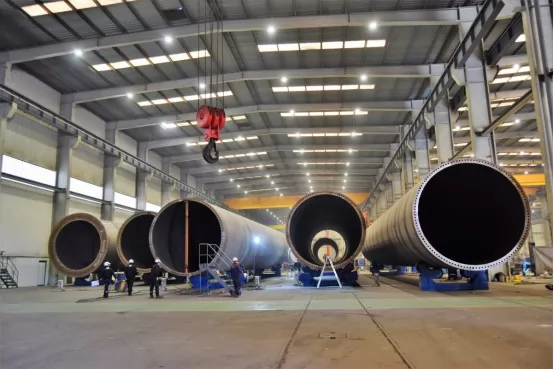
7. Advantages of Comprehensive Automation in Wind Tower and Foundation Pipe Production
-
Productivity and Consistency Through Automation: With automated processes, welding rotators and manipulators ensure uniformity, producing repeatable and highquality welds. This consistency reduces production downtime and increases throughput, making the production process efficient and scalable.
-
Reduced Labor Costs and Safety Enhancements: Automation minimizes the need for manual handling, reducing labor costs and improving worker safety. Remotecontrolled equipment and automated welding significantly decrease operator exposure to high temperatures, fumes, and physical strain.
-
Optimized Resource Use and Cost Savings: Automated welding and inspection systems minimize material wastage, energy consumption, and rework. Enhanced firstpass yield rates translate to direct cost savings and resource conservation, contributing to a sustainable manufacturing model.
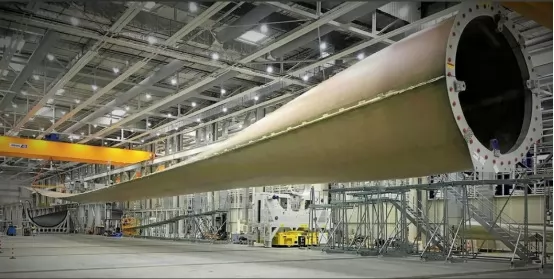