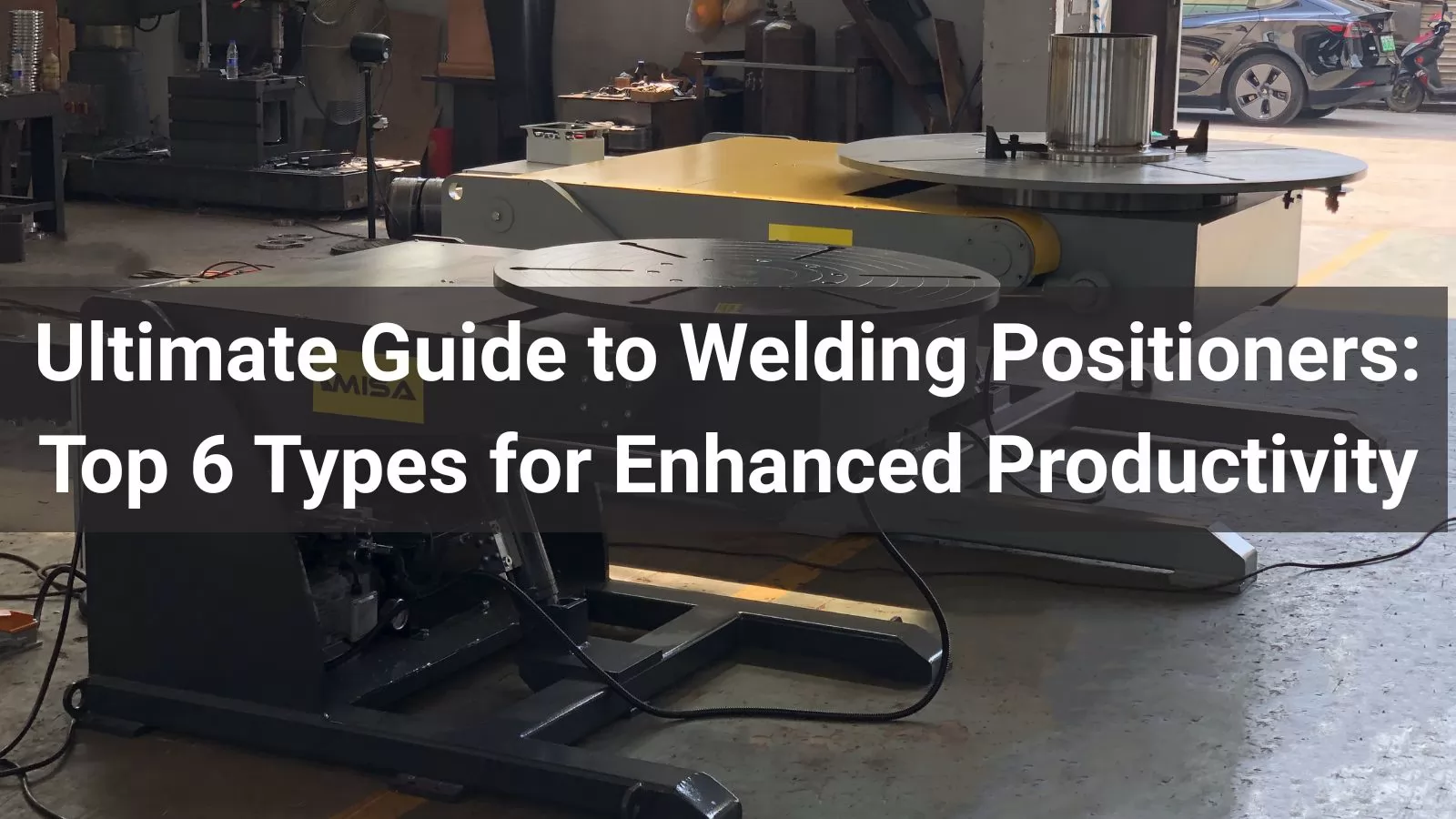
Introduction
In the world of modern welding, productivity and precision are key. One of the essential tools that can significantly enhance both of these factors is the welding positioner. These devices are designed to hold, rotate, and position workpieces, allowing welders to achieve optimal angles for more efficient and accurate welding. Whether you're working in a small-scale workshop or a large industrial facility, the right welding positioner can make a significant difference in your output.
This guide will explore the top six types of welding positioners: hydraulic, magnetic, rotary table, arc welding tables, AC precision, and heavy-duty. By understanding the unique benefits and applications of each, you can make an informed decision on which one is right for your welding needs, improving both safety and performance on the job.
1. Hydraulic Welding Positioners
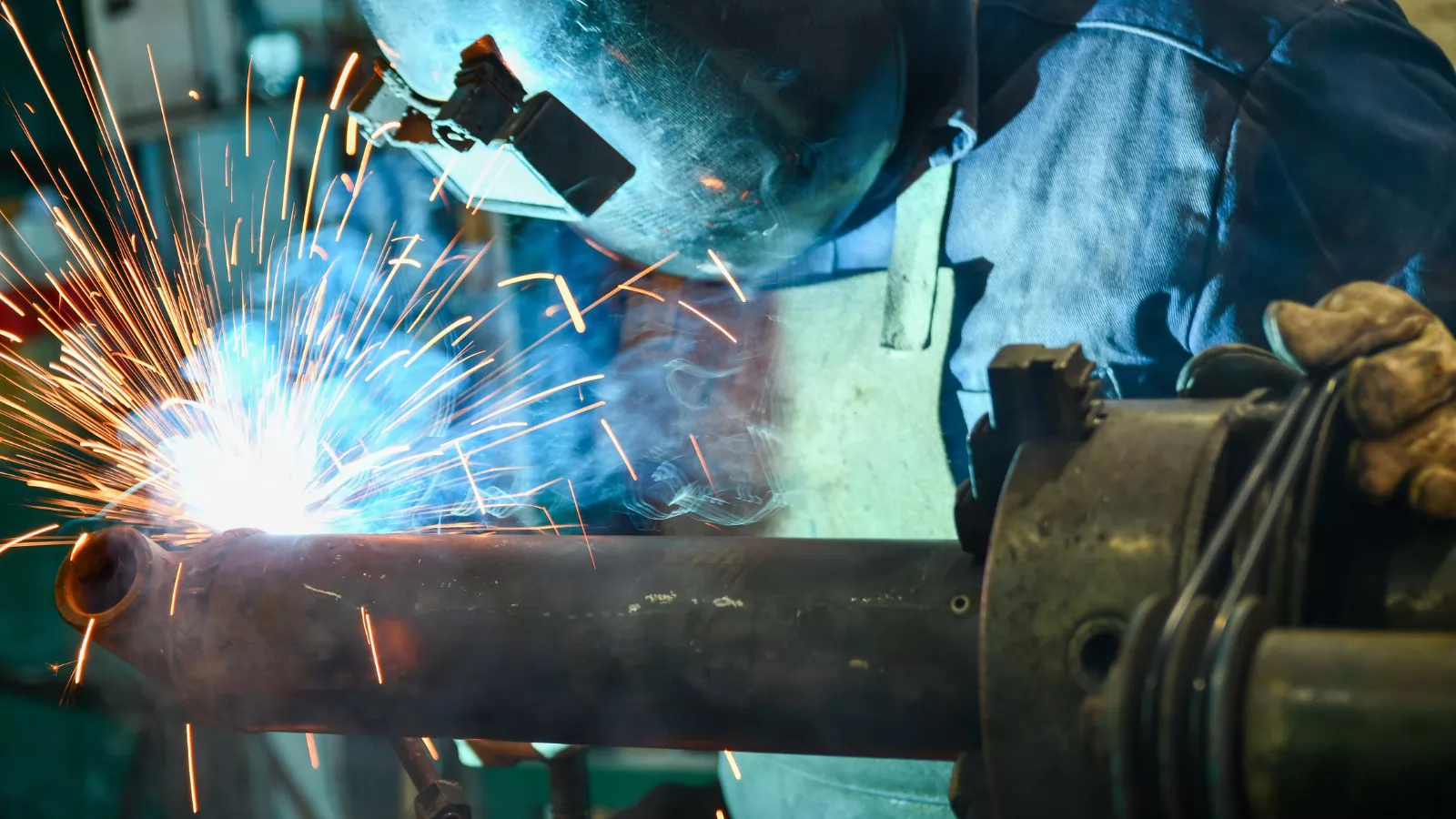
Hydraulic welding positioners use hydraulic systems to rotate and tilt the workpiece, providing excellent stability and control during the welding process. These positioners are known for their ability to handle heavy loads and provide precise movement, making them ideal for large and complex welding projects.
-
Mechanism and Benefits: Hydraulic positioners utilize hydraulic cylinders to adjust the position of the workpiece. This system allows for smooth, adjustable rotation and tilting, even under heavy loads. The power of hydraulics ensures that large and awkwardly shaped pieces can be welded with ease, enhancing overall workflow.
-
Ideal Applications: Hydraulic positioners are particularly useful in industries such as aerospace, shipbuilding, and heavy equipment manufacturing, where heavy, large, or uniquely shaped parts need to be welded. They are especially beneficial when high load capacities and precise, adjustable positioning are required.
2. Magnetic Welding Positioners
Magnetic welding positioners are compact and versatile tools that utilize powerful magnets to hold and rotate workpieces during the welding process. These positioners are known for their ease of use and quick setup, making them ideal for lighter projects and operations where space is limited.
-
How They Work: Magnetic positioners employ strong magnetic fields to securely hold workpieces in place while they are rotated. The magnets create a stable bond with ferrous materials, enabling precise positioning with minimal effort. This system offers fast setup times, which is particularly beneficial in high-volume, repetitive welding tasks.
-
Safety Considerations: While magnetic positioners are efficient, it’s important to take safety precautions. The powerful magnets can attract nearby ferrous materials, posing a risk of injury if not handled carefully. Operators should wear appropriate protective equipment and ensure the area is clear of unnecessary metal objects to avoid accidents. Additionally, it’s essential to check the strength of the magnet regularly to ensure secure attachment during use.
3. Rotary Table Welding Positioners
Rotary table welding positioners are designed to provide precise and controlled rotation for welding operations. These positioners are often used in automated welding systems where consistent rotation is needed to achieve high-quality welds.
-
Design and Functionality: Rotary table positioners typically feature a flat rotating surface, allowing the workpiece to be placed in an optimal position for welding. The rotation is powered either manually or via motorized systems, depending on the specific design. Some models may also include tilting features to adjust the workpiece’s angle during welding.
-
Use Cases in Automation: Rotary table welding positioners are widely used in automated welding environments where speed, consistency, and precision are required. These positioners are commonly found in industries such as automotive manufacturing, pipe welding, and large-scale fabrication. They ensure that workpieces are always held in the correct position, reducing human error and enhancing weld quality in mass production settings.
4. Arc Welding Tables with Positioners
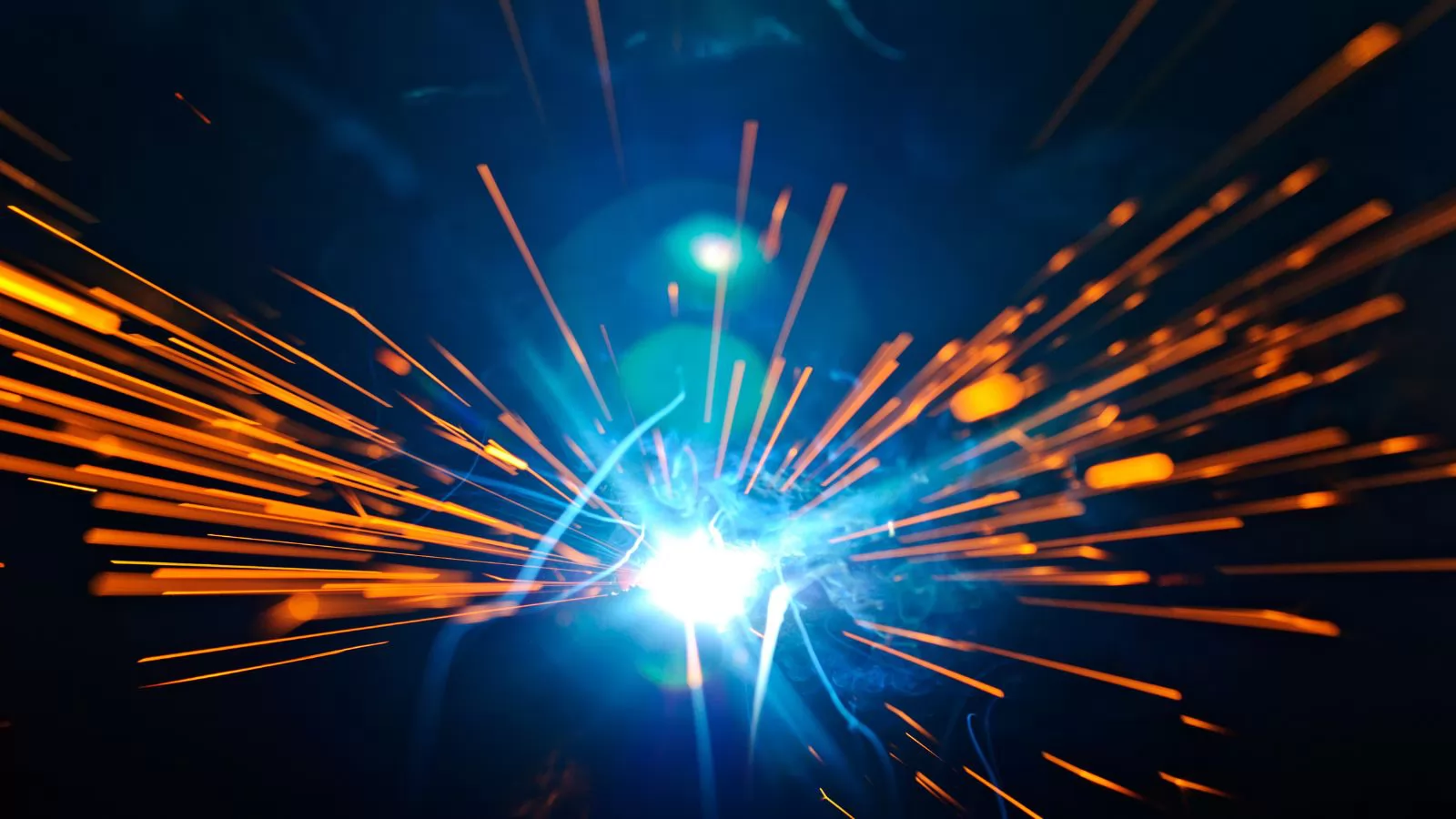
Arc welding tables with integrated positioners combine the benefits of a sturdy welding table with the positioning capabilities of a dedicated positioner. These systems are designed to enhance precision and productivity in arc welding applications, offering a stable surface and the ability to position workpieces at the ideal angle for welding.
-
Integration with Arc Welding: Arc welding tables with positioners allow for seamless integration with arc welding techniques. The workpiece can be easily rotated or tilted, ensuring optimal angles for the welder. This integration reduces the need for manual adjustments and enhances the overall efficiency of the welding process, especially when working with complex geometries or hard-to-reach areas.
-
Advantages in Precision Welding: These positioners provide exceptional accuracy, making them ideal for high-precision welding tasks. The stability of the welding table, combined with the precise positioning capabilities of the positioner, ensures that each weld is placed with consistency and minimal distortion. This is particularly useful in industries such as aerospace and electronics, where high-quality, precise welds are required.
5. AC Precision Welding Positioners
AC precision welding positioners are designed to provide precise control over the workpiece, often used for tasks that require exact positioning and stability. These positioners are equipped with alternating current (AC) motors to ensure smooth, steady motion during the welding process, making them ideal for high-precision applications.
-
Features and Specifications: AC precision welding positioners typically feature AC motors that offer precise, controlled rotation. These systems are designed for accuracy and repeatability, with features such as variable speed controls, adjustable tilt mechanisms, and robust support for heavy workpieces. The AC motor provides a smooth and consistent operation, ensuring that the workpiece stays in the ideal position throughout the welding process.
-
Suitability for Various Industries: AC precision positioners are ideal for industries that require high-quality, detailed welds, such as electronics, automotive, and medical device manufacturing. These positioners offer the precision needed for intricate welding projects and are especially beneficial when working with small or delicate parts where consistency and fine control are crucial.
6. Heavy-Duty Welding Positioners
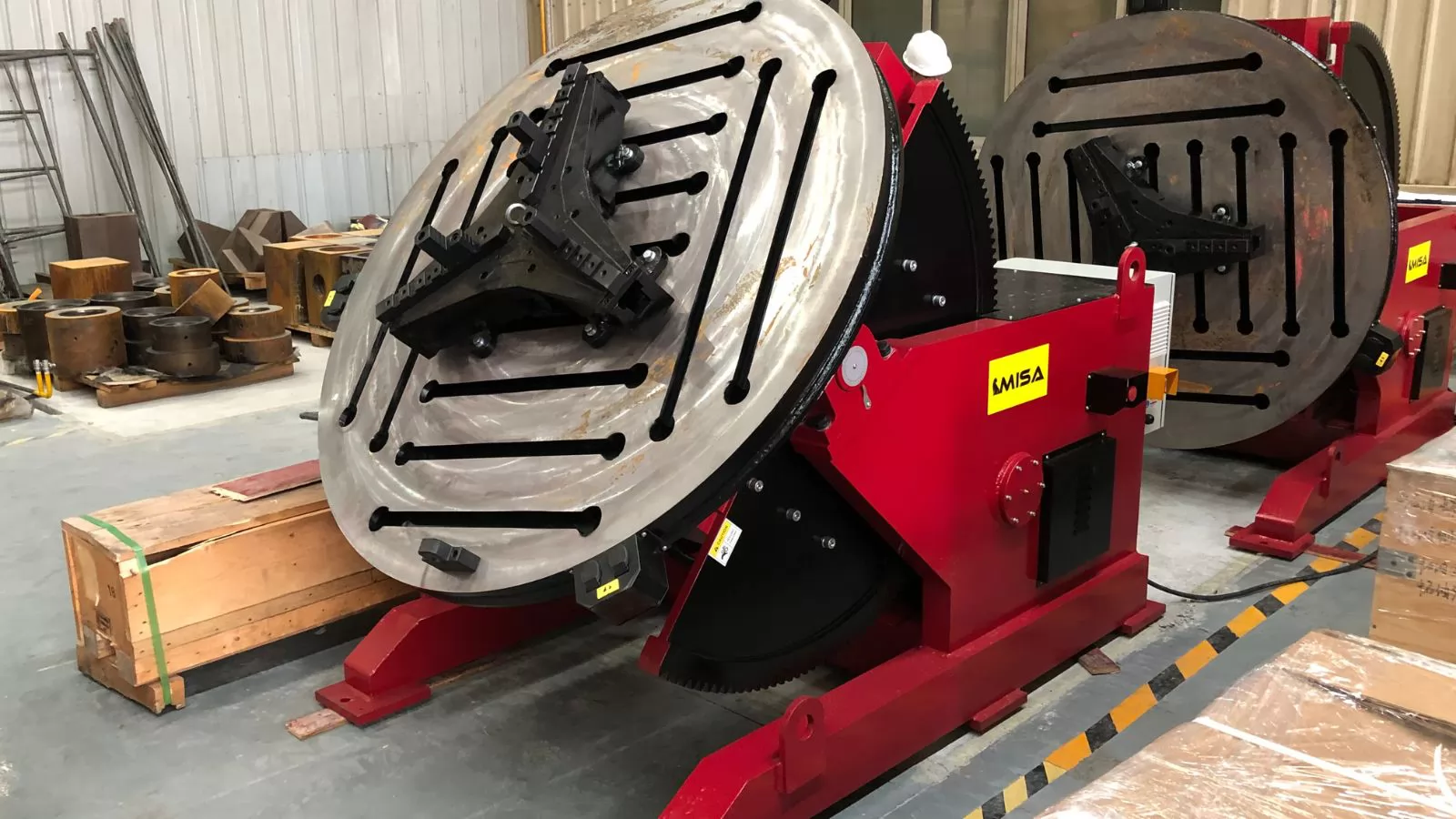
Heavy-duty welding positioners are built to handle large, heavy workpieces that require significant support and stability during welding. These positioners are designed for high-load capacities and are often used in industries where large-scale projects, such as construction, shipbuilding, or heavy equipment manufacturing, are common.
-
Handling Large-Scale Projects: Heavy-duty welding positioners are designed to rotate and tilt large workpieces without compromising stability or accuracy. These positioners are often equipped with powerful motors and robust construction to handle the weight and size of the materials being welded. This ensures smooth operation, even under the most demanding welding conditions.
-
Enhancing Safety and Efficiency: One of the key benefits of heavy-duty welding positioners is the enhanced safety they offer. By securely holding large workpieces in place and ensuring controlled movement, these positioners reduce the need for manual handling, minimizing the risk of accidents. Additionally, they boost efficiency by reducing setup time and enabling faster, more accurate welds, which is crucial in large-scale production environments.
Choosing the Right Welding Positioner
With so many different types of welding positioners available, choosing the right one for your specific needs can be a challenging task. Several factors must be considered to ensure you select a positioner that enhances both your workflow and the quality of your welds. Below are some of the key factors to keep in mind when making your decision.
-
Factors to Consider:
-
Workpiece Size and Weight: Ensure that the welding positioner you choose can support the size and weight of your workpieces. Heavy-duty positioners are best for large, bulky materials, while lighter models are suitable for smaller, less complex parts.
-
Precision Requirements: If your project demands high precision, you may want to opt for a precision positioner, such as an AC precision or arc welding table positioner, that offers fine control and accuracy.
-
Automation Compatibility: Consider whether the positioner will need to integrate with automated systems. Rotary table positioners and hydraulic systems are often compatible with automated setups, increasing productivity in high-volume environments.
-
Cost vs. Benefit Analysis: While cost is always a consideration, it’s important to evaluate the long-term benefits that a positioner will provide. Investing in a higher-quality positioner may reduce manual labor, enhance safety, and improve welding accuracy, all of which can lead to increased productivity and reduced errors over time.
Maintenance and Safety Tips
To ensure your welding positioner remains in optimal working condition and provides safe operation, regular maintenance and safety precautions are essential. Proper care and safety measures not only extend the lifespan of the equipment but also protect operators from potential hazards.
-
Regular Upkeep Practices:
-
Lubrication: Regularly lubricate the moving parts of the welding positioner to prevent wear and tear. This helps ensure smooth operation and reduces friction that could lead to mechanical failure.
-
Inspection: Perform regular inspections to check for signs of wear, such as cracks, corrosion, or loose components. Inspect the hydraulic system, motors, and electrical components, depending on the type of positioner.
-
Cleaning: Keep the welding positioner clean by removing welding debris and dust from the surface and components. This prevents buildup that can cause the equipment to malfunction.
-
Ensuring Operator Safety:
-
Training: Ensure that all operators are properly trained in the safe use of welding positioners. They should be familiar with the machine’s features, as well as the safety procedures specific to the equipment.
-
Protective Gear: Operators should wear the appropriate personal protective equipment (PPE), such as gloves, welding masks, and steel-toed boots, to reduce the risk of injury during operation.
-
Emergency Stops: Make sure the welding positioner is equipped with an easily accessible emergency stop function. This allows operators to quickly halt the machine if a hazardous situation arises.
Innovations in Welding Positioners
As with many other industries, welding positioners have benefited from advances in technology. These innovations have led to improved functionality, efficiency, and precision, further enhancing the welding process and making it easier for manufacturers to meet increasing production demands.
-
Technological Advancements:
-
Smart Positioning Systems: Modern welding positioners now often feature smart technology, such as sensors and automated controls, that can adjust the positioner’s speed, angle, and rotation based on real-time data. These systems can automatically correct any inconsistencies, improving weld quality and reducing human error.
-
Integration with Robotic Systems: Some positioners now integrate seamlessly with robotic welding arms, creating a fully automated welding solution. This integration allows for increased efficiency, especially in high-volume production environments, as robots can weld parts with little to no human intervention while the positioner ensures optimal positioning.
-
Energy-Efficient Motors: Advances in motor technology have led to more energy-efficient positioners, which consume less power while still providing powerful, reliable performance. These systems are not only more environmentally friendly but can also reduce operating costs over time.
-
Future Trends:
-
Artificial Intelligence (AI) Integration: In the future, AI may play a larger role in the operation of welding positioners. By analyzing data from sensors and cameras, AI could help optimize weld quality and positioner performance in real-time, creating even more intelligent systems.
-
Autonomous Positioning: The future may see more autonomous welding positioners that require minimal human intervention. These systems would use advanced algorithms and machine learning to automatically adjust to various welding scenarios, making the process more efficient and adaptable.
Case Studies
Real-world applications of welding positioners showcase the significant benefits these tools offer in various industries. These case studies provide insights into how welding positioners improve efficiency, precision, and safety, helping businesses achieve higher-quality welds while minimizing costs and downtime.
-
Real-World Applications:
-
Aerospace Industry: In aerospace manufacturing, welding positioners are crucial for assembling and welding large and complex components, such as aircraft fuselages and engine parts. Hydraulic and rotary table positioners are often used to ensure precise alignment and optimal welding angles, which is critical for meeting strict aerospace quality standards.
-
Shipbuilding: In shipbuilding, heavy-duty welding positioners are used to weld large metal sheets and structural components. These positioners are designed to handle the size and weight of ship hulls and other parts, ensuring that welding operations are performed quickly and accurately, even in challenging environments.
-
Automotive Manufacturing: In the automotive industry, robotic welding systems often work alongside rotary table positioners to assemble parts for vehicles. The integration of these systems results in fast, automated welding processes, improving both the speed and quality of production.
-
Success Stories:
-
Company X: A manufacturing company that implemented a hydraulic welding positioner in their production line saw a 30% increase in welding efficiency, reducing the need for manual handling and ensuring better weld quality on large metal parts.
-
Company Y: A shipbuilding company replaced their manual welding setups with heavy-duty positioners and noticed a significant improvement in safety and productivity. The ability to rotate and tilt large parts reduced worker strain and minimized errors, leading to fewer rework cycles.
FAQs
Below are some common questions about welding positioners and their usage, along with expert answers to help you make informed decisions about which positioner is best for your needs.
-
What is the main advantage of using a welding positioner?
The primary advantage of using a welding positioner is the improved efficiency and precision it brings to the welding process. Positioners allow for optimal positioning of the workpiece, reducing the need for manual adjustments and ensuring consistent weld quality. This ultimately increases productivity and reduces the likelihood of errors or defects.
-
Can a welding positioner be used for all types of materials?
Welding positioners can be used for a wide range of materials, but it is important to choose the right type of positioner based on the material being welded. For example, magnetic positioners work best with ferrous metals, while hydraulic and rotary positioners can handle a variety of materials, including heavier metals like steel and aluminum.
-
How do I know which welding positioner is right for my project?
The right welding positioner depends on several factors, including the size and weight of the workpiece, the type of welding required, and the need for automation. It’s important to assess your specific needs and choose a positioner that offers the necessary support, precision, and compatibility with your workflow.
-
Are welding positioners compatible with robotic systems?
Yes, many modern welding positioners are designed to integrate seamlessly with robotic welding systems. Rotary table positioners, in particular, are commonly used in automated welding setups, where they work in tandem with robotic arms to provide accurate and consistent welds in high-volume production environments.
Conclusion
Welding positioners are invaluable tools for improving the efficiency, accuracy, and safety of the welding process. Whether you're working with large, heavy components or need precision for smaller, intricate parts, there is a welding positioner designed to meet your needs. From hydraulic to magnetic, rotary table to heavy-duty options, each type offers unique advantages that can help streamline operations and boost productivity.
By understanding the different types of welding positioners, their features, and their applications, you can make an informed decision that will optimize your welding process. Remember to consider factors such as the size and weight of your workpieces, the precision required, and the compatibility with your automation systems when choosing the right positioner for your project.
Finally, always prioritize safety and maintenance to ensure your welding positioner performs at its best for years to come. With proper care and attention, a welding positioner can be a long-term asset, enhancing your welding operations and contributing to the success of your projects.