Welding manipulators are integral to automated pipe welding, providing precision and efficiency for various welding requirements, including inner and outer circumferential welds, longitudinal seams, and fillet welds. Designed for both heavy-duty and high-precision applications, the column and boom manipulators cater to diverse industry needs, particularly in pipelines used for gas, oil, and water transport.
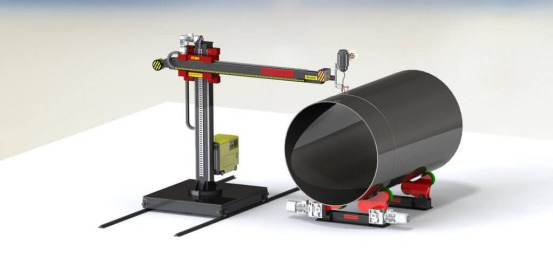
Structure and Mechanism of the Column and Boom Welding Manipulator
The column and boom welding manipulator is typically composed of:
-
Column: This supports the entire vertical structure and provides a stable base for lifting the boom.
-
Boom: The boom extends horizontally, allowing flexibility in reaching different positions along the welding line. It is equipped with a telescopic feature, which enables an extended reach and precise adjustments for different pipe sizes.
-
Slewing Mechanism: Allows for rotation of the column for flexible positioning of the welding torch, aiding in comprehensive coverage.
-
Trolley: Mounted on a standard track, the trolley can move horizontally, positioning the welding manipulator across the workspace.
The entire system is engineered for stability, durability, and adaptability to accommodate varying pipe sizes and welding angles.
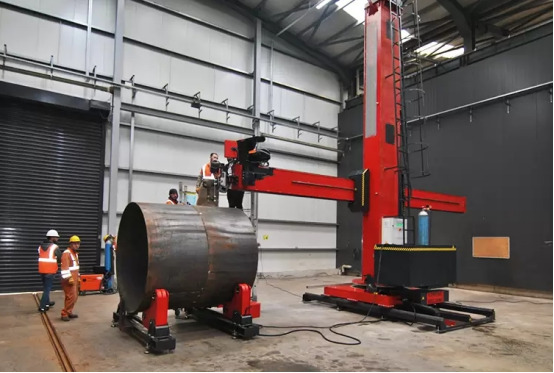
Welding Processes with the Column and Boom Manipulator
This manipulator supports various welding processes to meet specific requirements of different welds:
-
Submerged Arc Welding (SAW): Frequently used for thicker pipes, SAW provides deep weld penetration, making it ideal for joining large-diameter pipes. The boom can be extended to guide the flux along the seam.
-
Gas Metal Arc Welding (GMAW or MIG): Suitable for thinner plates and less demanding welds, GMAW offers a faster welding speed, ideal for less intensive weld seams.
-
Gas Tungsten Arc Welding (GTAW or TIG): Often employed for more refined welds, particularly on pipes requiring minimal heat input, like stainless steel. The precise control of GTAW is enhanced by the manipulator’s stable platform.
-
Flux-Cored Arc Welding (FCAW): Commonly used for pipes with medium thickness, FCAW provides a balance between deep penetration and weld quality.
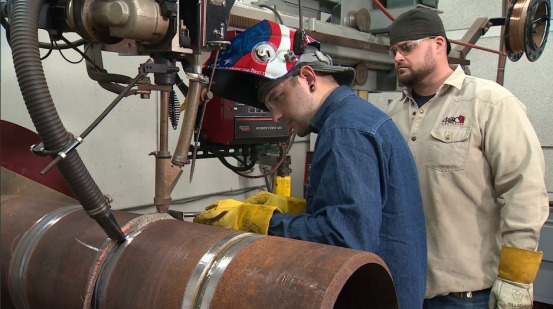
Handling Different Plate Thicknesses
Pipes vary widely in thickness depending on their purpose:
-
Thick Plates: For thicker pipes, such as those in gas and oil transport, SAW is the preferred choice. This process generates a strong weld, suitable for withstanding the pressure and flow of fluids. The manipulator provides consistent positioning and allows for precise heat and speed adjustments, minimizing weld defects.
-
Medium Thickness Plates: FCAW or GMAW processes are typically used. FCAW is especially useful for pipes with moderate wall thickness, where some degree of penetration and a moderate deposition rate are needed.
-
Thin Plates: GMAW or TIG welding processes are favored for thinner pipes, as they generate less heat, reducing the risk of distortion. The boom manipulator’s controlled movement aids in applying a precise weld seam, which is critical in applications with high standards for leak-proof seals.
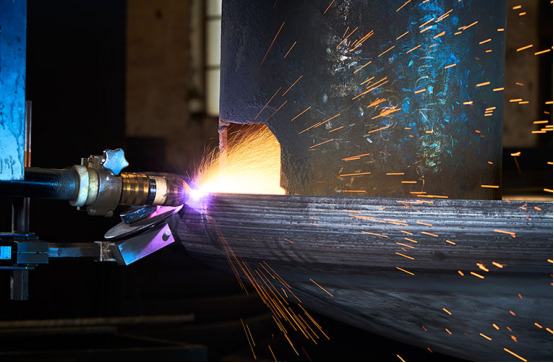
Integration with the Welding System
Column and boom manipulators integrate seamlessly with various other components in a welding system:
-
Welding Rotator: Often used in combination with the manipulator, a welding rotator provides rotational support to pipes, allowing the workpiece to rotate at a steady speed while the welding head remains stationary. This integration enhances the accuracy of circumferential welds and reduces manual handling.
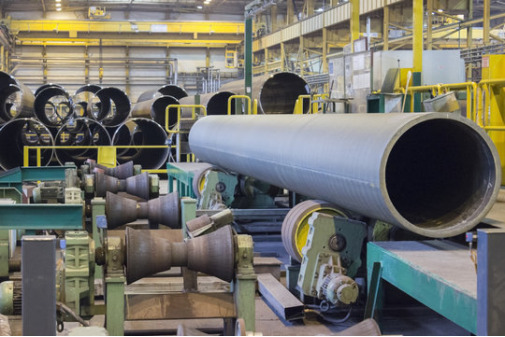
-
Welding Positioner: Used for positioning the pipe at specific angles for difficult weld seams. The welding manipulator and positioner work in tandem, allowing complex multi-angle welds without repositioning the pipe manually.
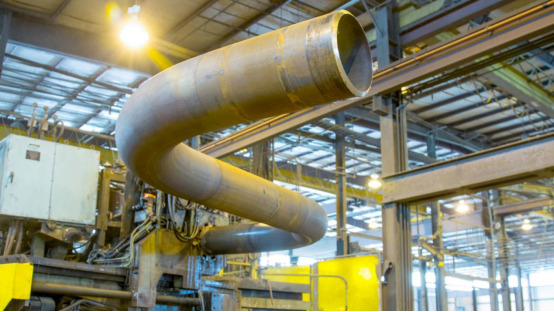
-
Control Systems: Advanced welding manipulators incorporate a user-friendly control system that includes both a near-control and remote-control box. Operators can adjust parameters like welding speed, torch angle, and travel distance, directly influencing weld quality. The manipulator’s interface often includes digital displays for speed and position, ensuring precision.
-
Safety and Monitoring Features: Safety is paramount in automated welding. The column and boom manipulator is equipped with anti-fall safety devices, high-precision gears for smooth rotation, and locking mechanisms for stability. Optional camera-based monitoring systems and sensors detect and correct misalignments during the welding process.
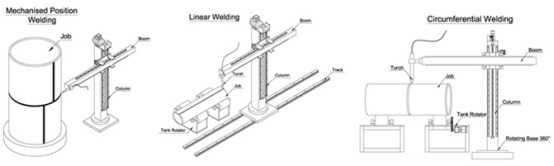
Automation and Process Control
Modern column and boom welding manipulators incorporate automation features that enhance process efficiency:
-
Automatic Seam Tracking: Ensures that the welding torch follows the weld seam accurately. This feature is particularly beneficial in maintaining consistent weld quality on large pipes where manual alignment is challenging.
-
Remote Welding Operation: Allows for full control from a distance, which is essential for hazardous or confined spaces. The remote control also minimizes operator fatigue by reducing the need for constant physical adjustments.
-
Data Logging and Analysis: The integration of data-logging features allows operators to monitor and analyze welding parameters such as temperature, speed, and voltage in real-time. This information is critical for quality assurance, enabling adjustments on the fly and ensuring compliance with industry standards.
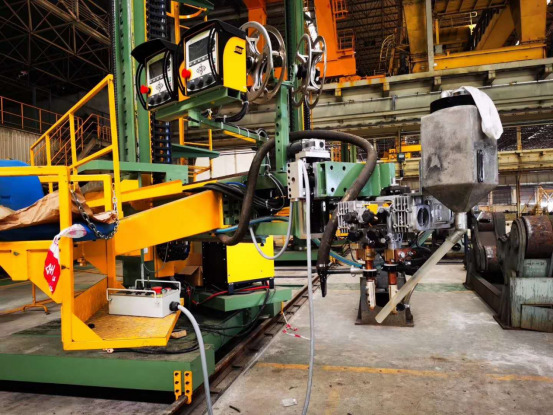
Applications in Industry
Column and boom manipulators are indispensable in various industrial applications:
-
Oil and Gas Pipelines: The manipulators facilitate welding large-diameter, thick-walled pipes, which are essential for transporting high-pressure gases and liquids over long distances.
-
Water and Wastewater Management: Manipulators are used to join pipes for municipal water supply and drainage systems, which demand robust and reliable welds to prevent leaks.
-
Industrial Plants: Within factories, these manipulators assist in fabricating process pipelines laid above ground for easy maintenance, which are often used in chemical plants and refineries.
-
Construction and Infrastructure: In the construction of bridges, tunnels, and other infrastructure, manipulators aid in welding heavy steel beams and large structural components, ensuring stability and longevity.
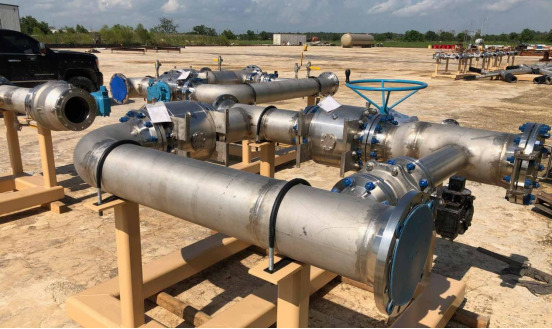
The column and boom welding manipulator serves as a critical component in the automation of pipe welding processes. By providing flexibility in positioning, stability in operation, and seamless integration with other welding equipment, it significantly enhances productivity, precision, and safety in welding tasks. Whether in the energy sector, infrastructure development, or manufacturing, this welding manipulator is an invaluable tool, offering tailored solutions for a wide range of pipe welding needs.
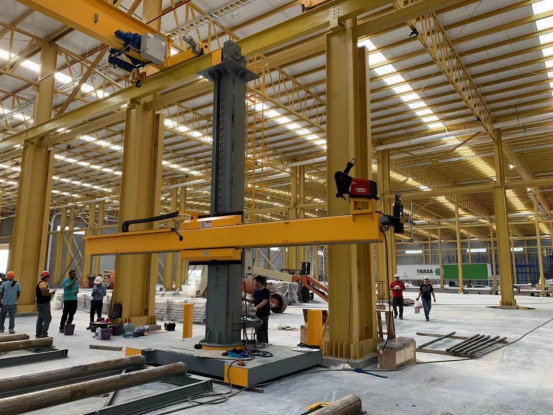