Heat Exchangers in Industrial Applications
Heat exchangers are pivotal in transferring thermal energy between fluids. This process plays a significant role in industries that require temperature control for operational efficiency and safety. Typical applications include:
-
Chemical Industry: Used in processes such as distillation, condensation, and reaction cooling. Heat exchangers help maintain specific temperatures to control reaction rates and ensure product consistency.
-
Petroleum Industry: Essential for refining processes, where crude oil undergoes heating and cooling phases. Exchangers aid in cracking, distillation, and product separation.
-
Power Generation: In thermal power plants, heat exchangers are used to condense steam and reuse it in the boiler, optimizing fuel efficiency.
-
Food Processing: Exchangers help in pasteurization and sterilization processes, maintaining the quality and safety of food products.
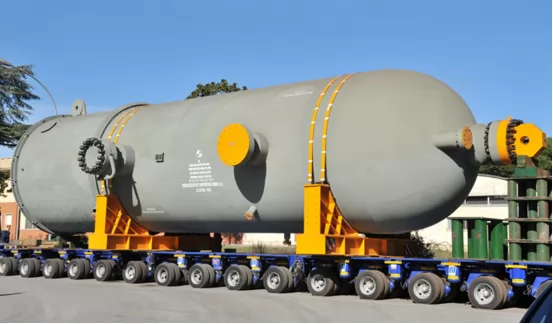
Classification of Heat Exchangers:
-
Partition Type: Utilizes a solid wall to separate fluids. Examples include shell-and-tube and plate heat exchangers, widely used for their high efficiency and ease of maintenance.
-
Hybrid Type: Allows partial mixing of fluids, suitable for applications where a controlled blend of fluids is beneficial.
-
Heat Storage Type: Temporarily stores heat in a medium before transferring it to another fluid. These are used in applications requiring cyclical or intermittent heating.
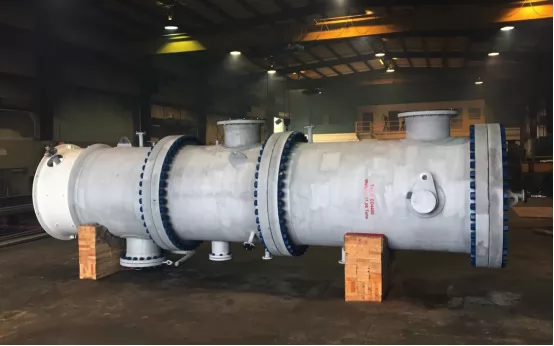
Material Selection for Heat Exchangers
Metals: Material choice depends on operating pressures, temperatures, and fluid corrosiveness:
-
Carbon Steel: Economical and suitable for low to moderate temperatures. It’s commonly used in water-to-water exchangers.
-
Stainless Steel: Resistant to corrosion, making it suitable for high-temperature and high-pressure environments. It’s widely used in chemical, food, and pharmaceutical industries for its non-reactivity and ease of cleaning.
-
Nickel and Nickel Alloys: High resistance to corrosion and oxidation at extreme temperatures, commonly used in petrochemical processes and high-pressure exchangers.
-
Titanium: Known for its exceptional corrosion resistance, often used in seawater or brine applications due to its durability and non-corrosive properties in saltwater environments.
-
Non-Metallic Materials: Certain applications involve non-metallic heat exchangers, especially in highly corrosive environments:
-
Ceramic Exchangers: Ideal for extreme temperatures and corrosive chemicals but typically more costly and less adaptable to high pressures.
-
Polymers: Lightweight and highly resistant to corrosion; however, their use is limited to lower temperatures and pressures.
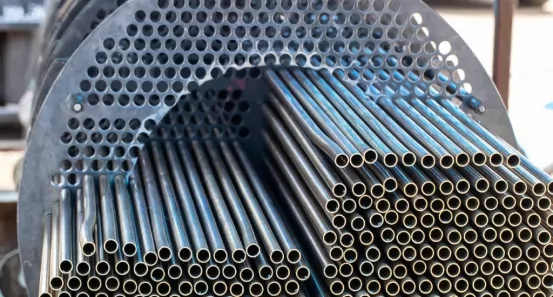
Heat Exchanger Corrosion and Maintenance Strategies
-
Corrosion Concerns: Heat transfer accelerates corrosion, especially under boiling or vaporizing conditions. The rate of corrosion also depends on the fluid medium (e.g., saline, acidic).
-
Corrosion Prevention Techniques:
-
Material Coatings: Applying coatings like epoxy or using cladding materials can extend equipment lifespan.
-
Corrosion Inhibitors: Adding specific chemicals to fluids to reduce corrosive interactions.
-
Electrochemical Protection: Methods like cathodic protection can reduce corrosion in aggressive environments.
-
Maintenance Protocols: Scheduled inspections and cleaning are essential to prevent residue build-up, which can lead to blockages, efficiency loss, and increased wear.
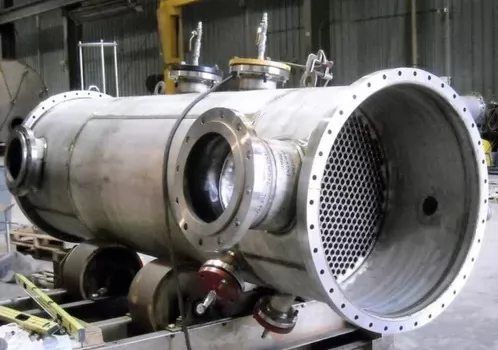
Welding Processes and the Role of Welding Rotators
-
Importance of Welding in Heat Exchanger Manufacture: Precise welding ensures structural integrity under high pressure and thermal stress. Different types of welding (e.g., TIG, MIG, and submerged arc welding) are selected based on material and design requirements.
-
Enhanced Stability: Rotators stabilize cylindrical components, ensuring even and consistent welds.
-
Reduced Manual Labor: Automated rotation minimizes manual adjustments, improving productivity and weld precision.
-
Surface Protection: Polyurethane rollers on rotators protect against scratches and maintain surface quality, especially crucial when handling polished or sensitive materials.
-
Versatility: Rotators can handle varying sizes and shapes, supporting multi-process production (welding, sandblasting, painting).
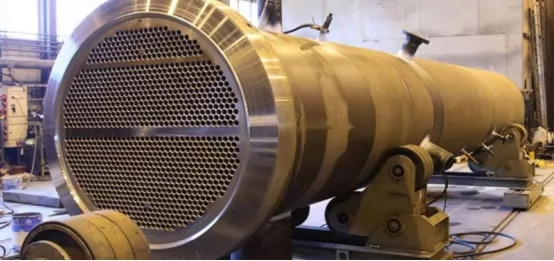
Specialized Applications of Heat Exchangers
-
Aerospace: Heat exchangers are essential for temperature regulation in fuel systems and environmental controls within aircraft.
-
Semiconductors: Critical in electronics manufacturing, where precise cooling is needed for chip production and assembly processes.
-
Wind Turbines: Oil coolers in wind turbine gearboxes ensure efficient operation.
-
Solar Power Plants: Used in thermal storage systems to transfer solar energy collected in the daytime for use during non-sunny hours.
-
Healthcare Equipment: In medical devices like MRI machines, exchangers help maintain temperature stability for operational accuracy and patient safety.
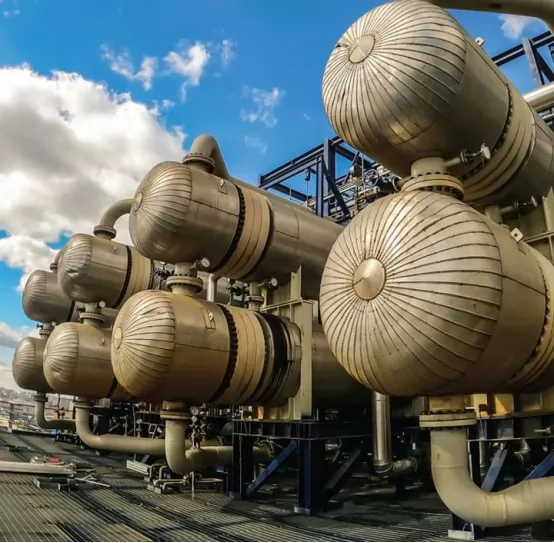
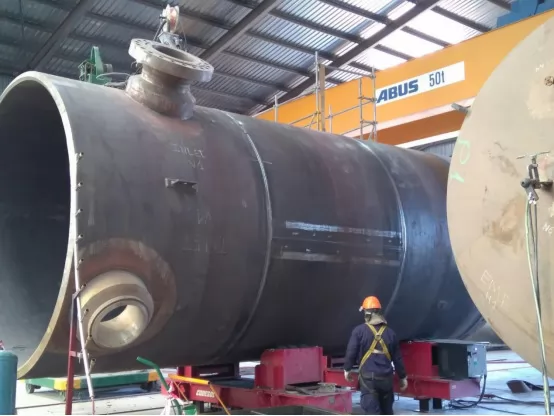
Manufacturing Process of Heat Exchangers
-
Material Preparation: This includes selection and verification of metal grades, which are then inspected for flaws.
-
Forming and Assembly: Includes processes like rolling and welding, where welding rotators play a key role.
-
Testing and Quality Assurance:
-
Pressure Testing: Ensures the exchanger can withstand operating pressures without leakage.
-
Nondestructive Testing (NDT): Techniques like ultrasonic testing and X-ray inspections detect internal flaws without damaging the product.
-
Final Assembly and Coating: For specific applications, a protective coating or finish may be applied to ensure longevity.
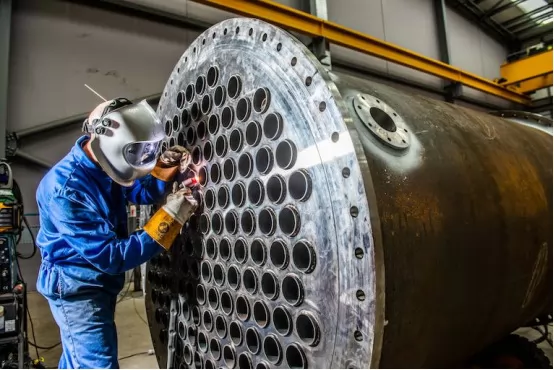
Advantages and Challenges of Using Heat Exchangers
Advantages:
-
Energy Efficiency: Heat recovery through exchangers reduces fuel and power consumption.
-
Process Optimization: Facilitates temperature control, which is critical for maintaining product quality and process stability.
-
Environmental Benefits: Lower energy use directly contributes to reduced greenhouse gas emissions.
Challenges:
-
Corrosion and Fouling: Frequent in high-temperature, high-pressure environments, corrosion and residue accumulation require regular maintenance and innovative design solutions.
-
Complex Manufacturing: The precision required for high-quality welding and material compatibility makes manufacturing labor-intensive and technologically demanding.
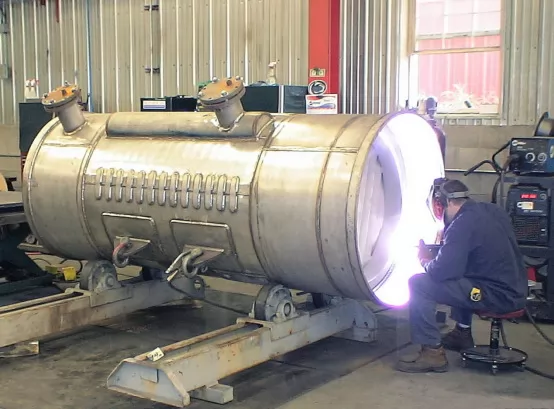
8. Future Trends in Heat Exchanger Technology
-
Advanced Materials: Development of composite materials that provide superior corrosion resistance and thermal conductivity.
-
Miniaturization: Especially in electronics and healthcare, smaller, highly efficient exchangers are needed.
-
Additive Manufacturing (3D Printing): Allows for complex geometries and customized heat exchanger designs that were previously impossible with traditional methods.
-
Smart Monitoring: Integration of IoT sensors to monitor performance and predict maintenance needs, reducing downtime and enhancing efficiency.
Application of Welding and Positioning Equipment in Heat Exchanger Production
In heat exchanger manufacturing, welding and positioning equipment are crucial in achieving high precision and meeting the demanding structural requirements. Here’s how various types of equipment contribute to the process:
1. Welding Rotators:
-
Function: Welding rotators provide stable and controlled rotation for cylindrical components, like shells and tube bundles, allowing welders to apply uniform welds. By supporting the workpiece, rotators reduce manual handling, increase productivity, and ensure consistent quality.
Benefits:
-
Surface Protection: Polyurethane rollers prevent scratches on the cylinder surface.
-
Efficient Welding: Controlled rotation allows for continuous welding, minimizing the need for start-stop welds, which can introduce weak points.
-
Applications: Besides welding, rotators are also valuable in processes like sandblasting, cleaning, and painting.
2. Positioners:
-
Function: Positioners hold the heat exchanger components in place, allowing precise orientation during welding. These are especially useful for large or irregularly shaped components that are difficult to rotate or move manually.
Benefits:
-
Improved Access: Positioners allow welders to access hard-to-reach areas, ensuring complete coverage and reducing the chance of weak joints.
-
Versatility: Positioners can be adjusted for various angles, which is beneficial in complex assemblies like U-tube and multi-tube exchangers.
-
Applications: Positioners are commonly used during the assembly and welding of tube bundles, tube sheets, and shell joints.
3. Welding Manipulators:
-
Function: Welding manipulators provide stable and adjustable support for welding torches, ensuring precise and steady welds. These can be manually or automatically adjusted to suit the heat exchanger’s configuration.
• Benefits:
-
Precision: Manipulators help maintain a consistent distance between the welding arc and the workpiece, crucial for achieving high-quality, uniform welds.
-
Safety: They reduce operator fatigue by supporting the welding tool, allowing operators to focus on controlling the welding process.
-
Applications: Manipulators are often used in long seam welding, especially in large shell-and-tube heat exchangers where precise weld alignment is critical.
4. Welding Fixtures and Clamps:
-
Function: Fixtures and clamps are essential for holding components securely in place during welding, ensuring that the pieces do not move under heat stress.
Benefits:
-
Accuracy: Prevents misalignment, which can lead to weak welds and costly rework.
-
Consistency: Standardizes positioning, especially useful for high-volume production.
-
Applications: Fixtures and clamps are used in the assembly of tube bundles and shell components, ensuring stability during welding.
Detailed Welding Process for Heat Exchangers
The welding process in heat exchanger production involves several specialized techniques, each selected based on material, component geometry, and design requirements. Here’s a step-by-step overview:
1. Preparation Stage:
-
Material Inspection and Preparation: All materials undergo inspection to ensure compliance with specifications. Surface cleaning is essential to remove contaminants like oil, rust, and oxides, which could weaken the weld.
-
Edge Preparation: Cutting, beveling, and preparing edges for welding create the right fit and angle for strong weld joints. For thick sections, multi-layer welds may be required, and proper edge preparation allows for easier control of each layer.
2. Common Welding Techniques in Heat Exchanger Production:
-
Tungsten Inert Gas (TIG) Welding:
-
Application: TIG welding is commonly used for stainless steel and non-ferrous metals like nickel alloys, providing precise control and high-quality welds.
-
Advantages: Offers clean welds with minimal spatter, which is crucial in applications where hygiene (e.g., food and pharmaceutical exchangers) and resistance to contamination are critical.
-
Metal Inert Gas (MIG) Welding:
-
Advantages: It’s faster than TIG and ideal for long seam welds, where speed and efficiency are priorities.
-
Application: MIG welding is often used for carbon steel and is suitable for high-speed welding in large assemblies.
-
Submerged Arc Welding (SAW):
-
Advantages: Delivers deep penetration and high weld strength, making it suitable for high-pressure applications.
-
Application: SAW is ideal for long, straight seams in thicker materials, such as the shells of large shell-and-tube heat exchangers.
-
Plasma Arc Welding (PAW):
-
Application: Used in applications requiring high precision, such as tube-to-tube sheet welding, where consistency and control are essential.
-
Advantages: Provides a narrow and focused arc, allowing for precise and deep welds, suitable for fine, detailed work.
3. Weld Quality Control and Inspection:
-
Visual Inspection: Initial checks for surface defects like cracks, porosity, and alignment issues.
-
Non-Destructive Testing (NDT):
-
Ultrasonic Testing (UT): Uses sound waves to detect internal flaws without damaging the component.
-
Radiographic Testing (RT): X-ray or gamma-ray inspections reveal hidden defects, ensuring weld integrity.
-
Dye Penetrant Testing (DPT): Effective for detecting surface cracks, particularly in non-magnetic materials like stainless steel.
-
Pressure Testing: Ensures that the welded component can withstand the operating pressures. Common methods include hydrostatic testing, where the exchanger is filled with water and pressurized to check for leaks.
4. Post-Welding Processes:
-
Heat Treatment: Certain materials require post-weld heat treatment (PWHT) to relieve residual stresses and improve structural integrity, especially in high-pressure exchangers.
-
Surface Finishing: Includes processes like sandblasting, grinding, and polishing. In applications where cleanliness is essential (e.g., food-grade exchangers), polished finishes prevent bacterial growth and contamination.
5. Automated Welding Systems:
-
In modern manufacturing, automated welding systems with robotic arms and programmable controllers are increasingly used. These systems offer precise control, repeatability, and high production speed, especially beneficial for large-scale production. Integration of automation with welding rotators and positioners maximizes efficiency and minimizes human error.
Advanced Applications of Welding Equipment in Specialized Heat Exchanger Production
1. Nuclear Power Plants:
-
High-specification welding equipment ensures the reliability of heat exchangers that operate in extreme temperatures and pressures within nuclear reactors.
-
Strict quality control with automated welding and robotic systems helps meet the stringent safety standards required.
2. Cryogenic Heat Exchangers:
-
For applications in liquefied natural gas (LNG) plants, where extremely low temperatures are involved, specialized welding techniques are needed to prevent material brittleness.
-
Welding positioners help ensure accurate positioning of parts during the process to avoid stress points that could lead to material failure at low temperatures.
3. Marine and Offshore Platforms:
-
Welding and positioning equipment are essential for the production of corrosion-resistant heat exchangers used in marine environments.
-
Welding rotators facilitate seamless welding of large exchangers that handle saltwater cooling, ensuring structural integrity under corrosive conditions.
4. Aerospace:
-
Heat exchangers in aerospace require precise welding for high-stress, lightweight materials like titanium alloys. Welding manipulators allow precise torch control, ensuring consistent and defect-free welds.
-
Positioners and rotators enable efficient welding in complex configurations, meeting the strict tolerances of aerospace applications.