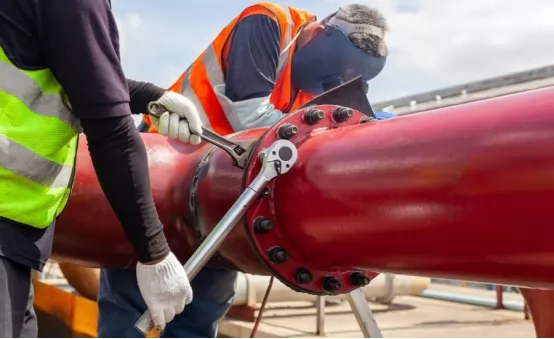
1. Overview of Welding Positioners in Flange, Pipe, and Elbow Welding
Welding positioners are crucial for the efficient and precise welding of pipe fittings, flanges, and elbows in pipeline manufacturing and construction. These positioners allow for controlled movement and positioning of workpieces, providing optimal access to welding seams. They enhance efficiency, improve weld quality, and reduce operator fatigue, especially when handling heavy or complex workpieces.
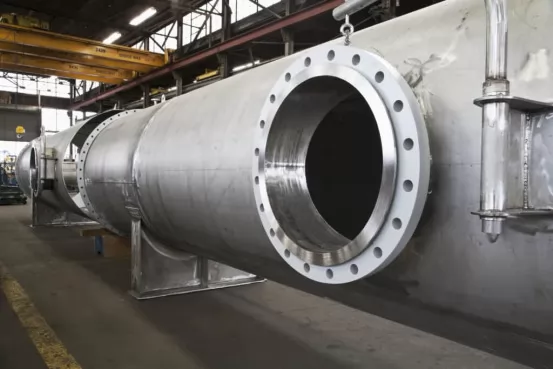
2. Types of Welding Positioners and Their Applications
Different welding positioners offer unique advantages depending on the workpiece and welding process requirements. Here’s a breakdown of commonly used positioners and their specific applications:
a. Rotary Welding Positioners
-
Rotary positioners are widely used for circular welding tasks. They hold the workpiece on a rotating table, allowing the welder to continuously weld around the circumference.
-
Ideal for flange and elbow welding, rotary positioners allow for even, uninterrupted welds around the perimeter.
-
Flanges can be fixed on the rotary table, typically using a suitable chuck or clamp to keep them secure. The operator can then rotate the flange for a continuous weld without needing to reposition the workpiece manually.
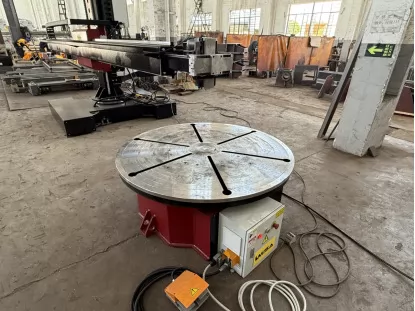
b. Tilt-Rotate Positioners
-
These positioners provide both tilt and rotation functions, giving the operator control over the workpiece’s angle.
-
Useful for welding elbows, which require precise angling, or for welding flanges at an angle on pipes.
-
The flange or elbow is secured on the tilt-rotate table, with clamps or specialized fixtures holding it in place. The tilting function is especially helpful when welding elbows that require multi-angle access.
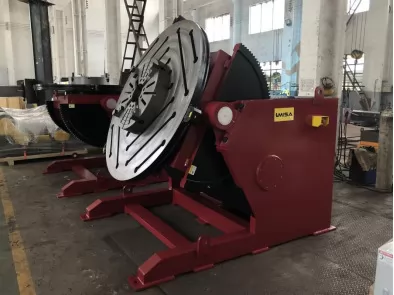
c. Headstock and Tailstock Positioners
-
These are designed to support long pipes by holding each end, allowing the workpiece to be rotated along its axis.
-
Particularly useful for welding long pipe sections and for applications where multiple flanges or elbows are to be welded along the same pipeline.
-
The headstock drives rotation, while the tailstock provides support and stability. Pipes are clamped securely to prevent shifting during welding, allowing for precise positioning along the length.
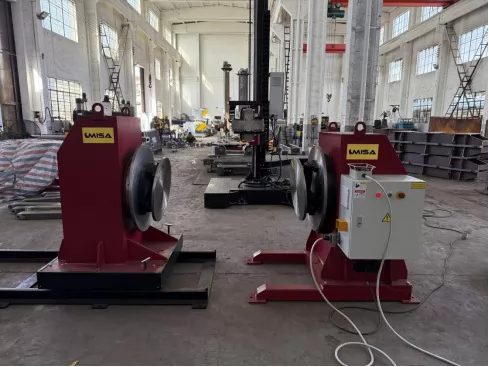
d. Single-Axis Positioners
-
Single-axis positioners rotate the workpiece in one direction only, often used for simpler or smaller welding tasks.
-
Suitable for welding smaller flanges or lightweight elbows where the movement is required only along a single plane.
-
This type of positioner simplifies the process for smaller workpieces, allowing operators to maintain a steady position while welding a straightforward seam.
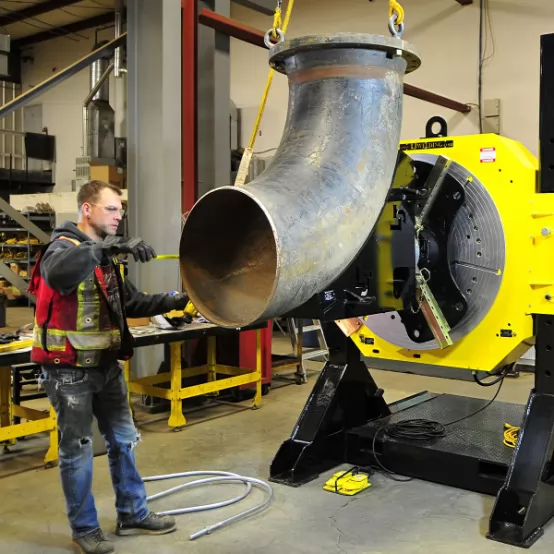
3. Welding Processes and Techniques
a. Flat Welding vs. Butt Welding for Flanges and Elbows
-
Flat Welding: Used primarily for low-pressure applications, flat welding connects the flange to the pipe with a single-sided weld. Flat welding positioners maintain the flange and pipe in a fixed position, allowing the operator to perform a shallow weld.
-
Butt Welding: For high-pressure applications, butt welding is performed with flanges and pipes aligned edge-to-edge, requiring dual-sided welds. This technique typically uses a positioner that can hold the pipe vertically and allow for tilting, providing better control over seam alignment and access.
b. Multi-Pass Welding for Elbows
-
Multi-pass welding involves multiple layers or “passes” of weld along the seam. Positioners are invaluable in multi-pass welding, providing stability and preventing the workpiece from moving between weld passes. For large-diameter elbows, tilt-rotate or rotary positioners enable multi-pass welds with precise control over seam angles.
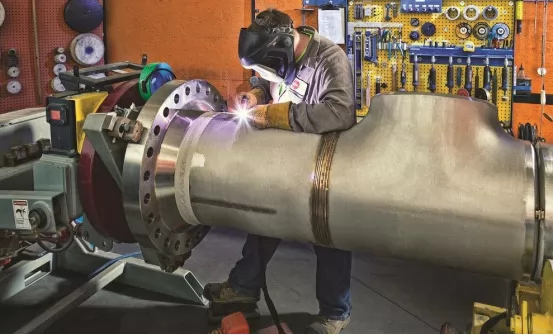
4. Assembly and Preparation
Before welding, it is essential to assemble the components accurately and secure them with appropriate fixtures:
a. Chucks and Clamps
-
Chucks: For rotary and tilt-rotate positioners, chucks are used to grip round workpieces like pipes and flanges securely. They offer a firm hold and prevent movement during welding. Three-jaw or four-jaw chucks are commonly used based on the workpiece size.
-
Clamps: Clamps are versatile and can secure flat surfaces or irregular shapes. Adjustable clamps allow for flexible positioning, ideal for holding the flange or elbow on a flat welding table.
b. Fixtures for Elbows and Irregular Shapes
-
Fixtures are designed to hold specific shapes, such as elbows with curved surfaces. Custom fixtures can be created to stabilize odd shapes and reduce movement. Using fixtures ensures consistency in weld placement and quality.
c. Alignment and Tack Welding
-
Before fully welding, components like flanges, elbows, and pipes are aligned on the positioner and secured using chucks, clamps, or fixtures. Tack welds are then applied to hold the parts in place, ensuring alignment is maintained during the main welding process.
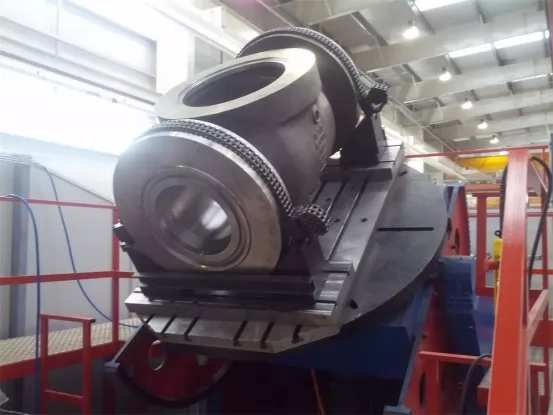
5. Using the Welding Positioner in Different Processes
a. Flange Welding Process
-
Setup: The flange is fixed on the positioner table using a chuck or clamp.
-
Welding: Rotary positioners are often used to rotate the flange, allowing continuous welds around the flange’s circumference.
-
Inspection and Adjustment: After welding, the flange can be inspected for weld consistency. The positioner’s rotation function ensures access to all angles for quality checks.
b. Pipe Welding Process
-
Setup: The pipe is placed between the headstock and tailstock positioners, with each end clamped securely.
-
Welding: The pipe rotates horizontally, allowing the welder to move along the seam without repositioning.
-
Post-Weld Treatment: The positioner can also aid in processes like grinding or sandblasting by rotating the pipe for uniform surface finishing.
c. Elbow Welding Process
-
Setup: The elbow is mounted on a tilt-rotate positioner, with a fixture providing stability.
-
Welding: The tilt-rotate function allows the elbow to be positioned precisely, enabling access to both interior and exterior seams.
-
Finishing: After welding, the elbow can be repositioned for any additional treatments, such as polishing or heat treatment.
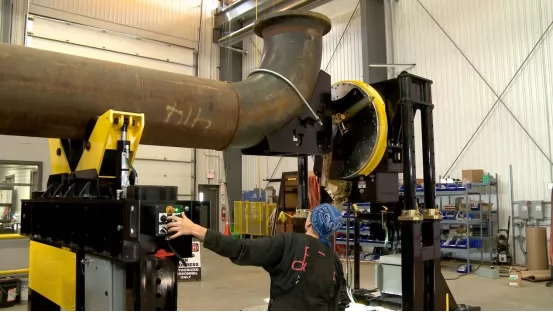
6. Additional Considerations
a. Safety and Ergonomics
-
Using a welding positioner minimizes manual handling of heavy workpieces, reducing fatigue and improving safety. The flexibility of the positioner to adjust workpieces at comfortable heights and angles also prevents repetitive strain injuries.
b. Customized Positioners for Specialized Needs
-
For specific applications, custom positioners can be built with additional degrees of freedom or tailored fixtures to handle complex shapes and sizes. For instance, large elbows may require a positioner with higher weight capacity or additional rotation axes.
c. Automation and Integration
-
Many positioners can be integrated with robotic welding systems for automated processes. This is particularly beneficial for high-volume welding in industries where speed and precision are essential.
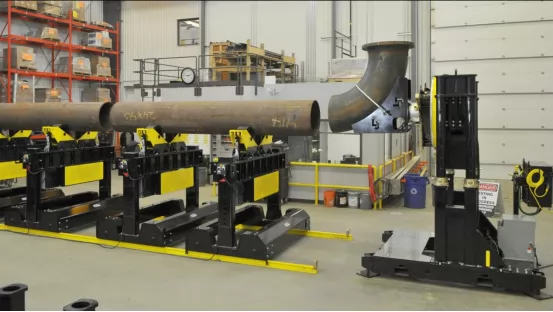
In summary, welding positioners provide invaluable assistance in welding flanges, pipes, and elbows. By offering controlled movement, secure clamping, and flexibility, these tools ensure high-quality, efficient welding for even the most challenging workpieces. Their versatility in various welding setups — from rotary and tilt-rotate to headstock and tailstock configurations — makes them indispensable in pipeline manufacturing and assembly. Custom fixtures, automated integration, and ergonomic design further enhance their role in producing strong, precise welds across the industry.
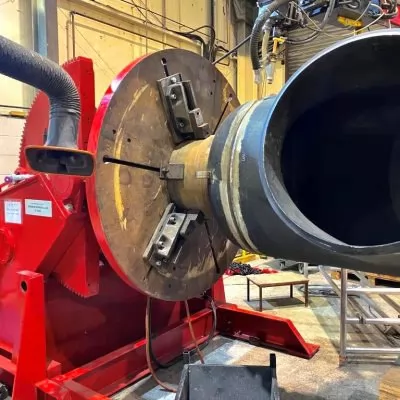