Welding Positioners for Dish Head and Customized Workpiece Handling
1. Introduction to Dish Head Welding and Customized Workpiece Handling
In manufacturing and heavy industry applications, welding and assembling end heads, such as dish heads, and customized workpieces are critical tasks. These components are integral in pressure vessels, storage tanks, and various types of machinery. The precise and safe handling of these parts is essential due to their large size, weight, and often complex shapes. Welding positioners play a crucial role in these processes, ensuring alignment, efficiency, and quality in the assembly and welding of dish heads and other specialized workpieces.

2. Welding Positioners for Dish Head Welding
Dish heads, characterized by their concave, bowl-like shape, are commonly used in pressure vessels and storage tanks to provide robust sealing and pressure distribution. Welding dish heads to cylindrical bodies requires meticulous alignment and steady positioning, as even slight misalignments can lead to weaknesses and failures in the welded seams. Here’s how welding positioners facilitate this process:
-
Positioning and Alignment: A welding positioner helps align the dish head with the cylindrical body or other components it is attached to. By adjusting the positioner’s tilt angle and rotation, welders can achieve a perfect alignment along the weld seam, minimizing the risk of deviations.
-
Rotation for Seamless Welding: Once positioned, the welding positioner can rotate the dish head and cylinder assembly smoothly, allowing for continuous welding along the seam. This is particularly advantageous for dish heads with long circumferential welds, as it allows the welder to maintain a consistent arc and heat distribution, reducing the risk of warping or uneven penetration.
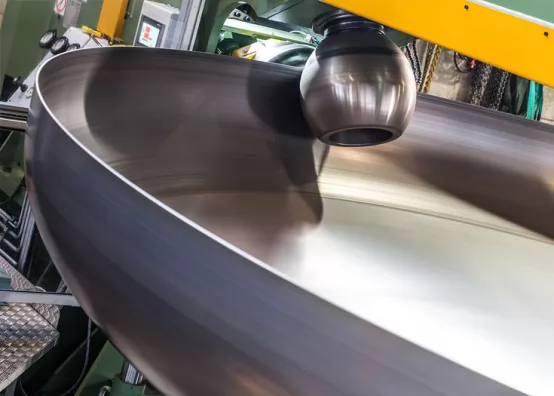
-
Reduction of Operator Fatigue: Given the large size and weight of dish heads, manual handling during welding would be challenging and potentially unsafe. The welding positioner not only holds the workpiece securely but also rotates and tilts it to the ideal welding position, reducing the physical strain on welders and allowing them to focus on weld quality.
-
Automatic vs. Manual Welding Options: Depending on the requirements, positioners can be used with both manual and automatic welding methods. For large, repetitive jobs, automatic submerged arc welding is often employed, providing high-quality, efficient welds with a uniform finish. Manual arc welding, on the other hand, is used for more intricate or customized dish heads where precise control is necessary.
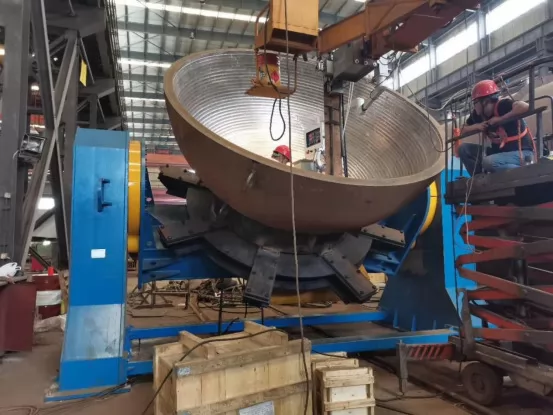
3. Assembling and Welding Customized Workpieces with Positioners
Customized workpieces vary greatly in shape, size, and weight, often creating unique challenges for welding and assembly. Positioners are tailored to meet these challenges, offering flexibility and precision to ensure these workpieces are securely held and accurately welded.
-
Adaptable T-Slot Tables and Chucks: Welding positioners designed for custom workpieces are often equipped with T-slot tables that allow for flexible chuck placement and workpiece clamping. This customization ensures the workpiece remains fixed in place, regardless of its irregular shape, allowing the operator to focus on optimal weld angles and precision.
-
Customizable Rotation and Tilting Angles: By using the hand control or programmable controls, operators can adjust the rotation speed, tilt angle, and position of the table to match the geometry of the customized workpiece. This is particularly useful for multi-pass welds, as it enables the welder to approach the weld joint from the most accessible angle for each layer, ensuring a strong, uniform weld.
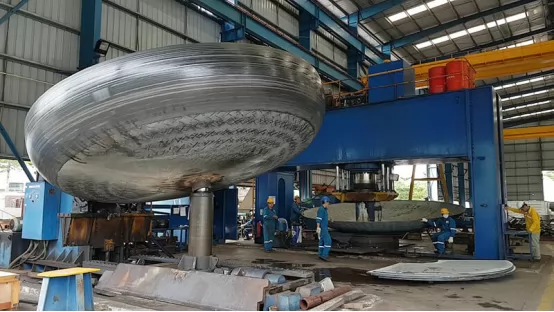
-
Handling Irregular Shapes: For irregularly shaped workpieces, positioners can be fitted with custom fixtures or tailored clamps that prevent movement during the welding process. This stability is essential to achieving accurate welds on parts that would be difficult to manipulate manually.
-
Improved Accessibility and Safety: With the workpiece securely mounted and positioned, welders have better access to difficult-to-reach areas without needing to move around the part or adopt uncomfortable positions. This enhances both the safety and productivity of the welding process, particularly for heavy or awkwardly shaped components.
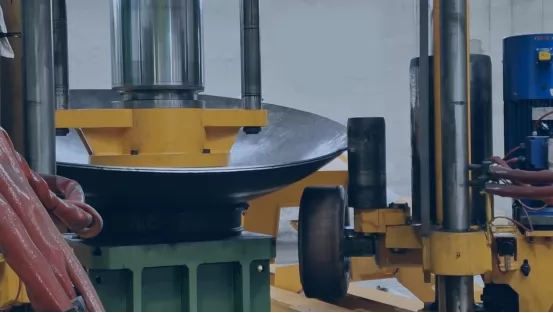
4. Application Scenarios for Dish Head and Customized Workpiece Welding
The use of welding positioners is widespread across several industries, including:
-
Petrochemical and Gas Industries: Dish heads used in high-pressure applications, such as storage tanks and chemical reactors, benefit from positioners that provide precise control over welding seams. This accuracy is essential to maintain the structural integrity and safety of the vessel under pressure.
-
Pharmaceutical and Food Processing: In industries with stringent cleanliness and quality standards, such as pharmaceuticals and food processing, welding positioners enable smooth, even welds without contamination. The consistent control over weld penetration and finish is crucial to prevent leaks and ensure sanitation.
-
Aerospace and Military Applications: Customized components with unique geometries, often required in aerospace and military applications, benefit from welding positioners that provide flexibility and precision. Positioners enable the welding of intricate shapes while minimizing the need for secondary adjustments or alignments.
-
Heavy Machinery and Construction: For heavy-duty equipment that involves customized assemblies, such as lifting platforms, cranes, and construction machinery, welding positioners enable efficient handling and precise welding of large, complex parts.
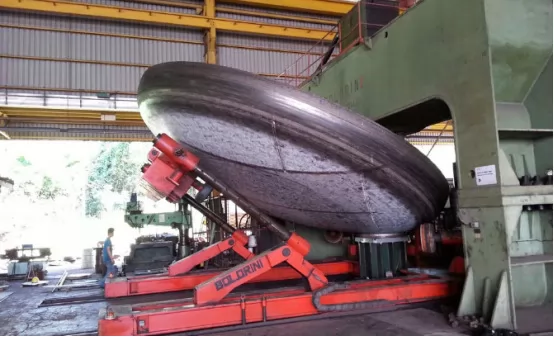
5. Welding Positioner Types for Dish Heads and Customized Components
MISA and other manufacturers offer various types of welding positioners that cater to different needs in dish head and custom workpiece applications:
-
Fixed Welding Positioners: Ideal for smaller, simpler parts that require basic rotation for circumferential welding. These positioners are robust and highly durable, suitable for repetitive tasks with consistent dimensions.
-
Hydraulic and Lifting Positioners: Used for larger or heavier components, hydraulic positioners allow for height adjustment and rotation, enabling welders to achieve the ideal working height and angle, even for substantial or cumbersome parts.
-
L-Shaped and Head-and-Tailstock Positioners: Designed for long or bulky items that require support on both ends, head-and-tailstock positioners maintain alignment while allowing rotation along the length of the workpiece. This design is particularly beneficial for pipes or extended assemblies where alignment across multiple weld points is necessary.
-
Customized Positioners: For uniquely shaped workpieces that standard positioners cannot handle, custom-built positioners provide tailored solutions. These may include specially designed chucks, fixtures, or even automated controls to meet the specific requirements of the project.
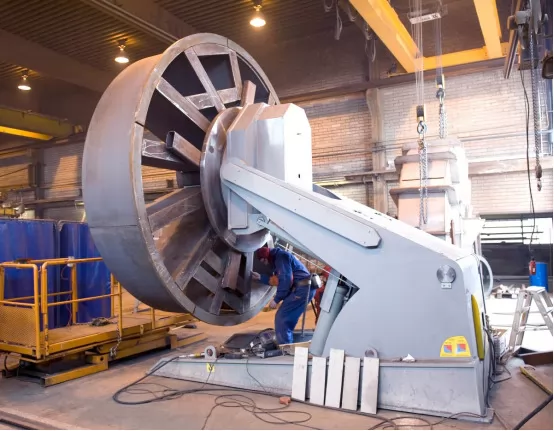
6. Conclusion
Welding positioners significantly improve the quality, safety, and efficiency of welding dish heads and customized workpieces. By enabling precise alignment, rotation, and handling of large, heavy, or irregularly shaped components, positioners support the high standards required across industries. Whether for pressure vessels in petrochemicals or specialized equipment in aerospace, the use of welding positioners ensures consistent and reliable results, reducing operator fatigue, enhancing productivity, and upholding the structural integrity of each welded assembly.
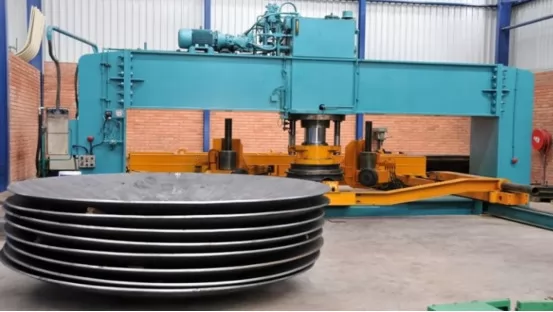